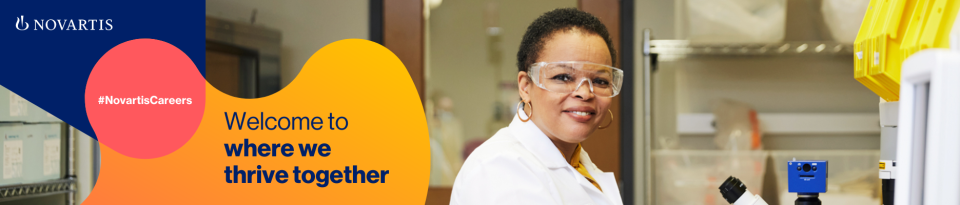
Job Description Summary
The Engineer, Manufacturing Science and Technology assists with the development and improvement activities for the cell culture, recovery,purification, and/or aseptic fill/finish manufacturing processes used to manufacture gene therapy products at a site.
Job Description
Responsibilities:
- Supports the collection and interpretation of continued process verification data and collaborate with other departments on manufacturing related issues to drive resolution and process improvements.
- Serve as a scientific and technical representative for process-related issues and investigations at the facility.
- Performs trending and monitoring of critical quality attributes/critical process parameters to maintain product quality and to control process drift.
- Supports tech transfer of new products and processes to ensure smooth transition from process development into GMP manufacturing.
- Looks for opportunities to implement operational excellence and continuous improvement.
- Partners with Quality to ensure a compliant manufacturing environment.
- Partners with manufacturing to meet the production schedule, ensure commercial supply and uphold quality standards, and participates in start-up efforts of new equipment, software or processes in manufacturing.
- Assists in documenting changes/updates to manufacturing processes and partner with manufacturing, engineering and validation to implement those changes.
- Provides technical/scientific support on project deliverables, i.e. remediation initiatives, plan reports.
- Completes requisite training, as well as applicable policies and procedures, related to the job function is an expectation to support ongoing manufacturing support.
Requirements:
- Bachelor's degree in biochemistry, chemical engineering, bioengineering, or related technical field with 4 years of experience in biopharmaceutical based GMP manufacturing operations including direct experience in cell culture, recovery, purification, and/or aseptic fill/finish, or related engineering field.
- Bachelor's degree in biochemistry, chemical engineering, bioengineering, or related technical field with 3 years of direct Novartis GTx experience.
- Master of Science degree in biochemistry, chemical engineering, bioengineering, or related technical field with 2 years of experience in support of biopharmaceutical manufacturing, or related engineering field.
- Familiar with global regulations on cGMP manufacturing of drug substance, drug products devices, validation/qualification requirements.
- Strong technical writing ability.
- Proven ability to effectively participate on teams.
Why Novartis: Our purpose is to reimagine medicine to improve and extend people's lives and our vision is to become the most valued and trusted medicines company in the world. How can we achieve this? With our people. It is our associates that drive us each day to reach our ambitions. Be a part of this mission and join us! Learn more here:
https://www.novartis.com/about/strategy/people-and-culture. The pay range for this position at commencement of employment is expected to be between $97, 600-146,400 annual; however, base pay offered may vary depending on multiple individualized factors, including market location, job-related knowledge, skills, and experience. The total compensation package for this position may also include other elements, including a sign-on bonus, restricted stock units, and discretionary awards in addition to a full range of medical, financial, and/or other benefits (including 401(k) eligibility and various paid time off benefits, such as vacation, sick time, and parental leave), dependent on the position offered. Details of participation in these benefit plans will be provided if an employee receives an offer of employment. If hired, employee will be in an "at-will position" and the Company reserves the right to modify base salary (as well as any other discretionary payment or compensation program) at any time, including for reasons related to individual performance, Company or individual department/team performance, and market factors. You can find everything you need to know about our benefits and rewards in the Novartis Life
Handbook. https://www.novartis.com/careers/benefits-rewards
#LI-hybrid
EEO Statement:
The Novartis Group of Companies are Equal Opportunity Employers and take pride in maintaining a diverse environment. We do not discriminate in recruitment, hiring, training, promotion or other employment practices for reasons of race, color, religion, gender, national origin, age, sexual orientation, gender identity or expression, marital or veteran status, disability, or any other legally protected status. We are committed to building diverse teams, representative of the patients and communities we serve, and we strive to create an inclusive workplace that cultivates bold innovation through collaboration and empowers our people to unleash their full potential.
Accessibility and reasonable accommodations
The Novartis Group of Companies are committed to working with and providing reasonable accommodation to individuals with disabilities. If, because of a medical condition or disability, you need a reasonable accommodation for any part of the application process, or in order to perform the essential functions of a position, please send an e-mail to tas.nacomms@novartis.com call +1 (877)395-2339 and let us know the nature of your request and your contact information. Please include the job requisition number in your message.
https://www.novartis.com/careers/careers-research/notice-all-applicants-us-job-openings
Salary Range
$97,600.00 - $146,400.00
Skills Desired
Assembly Language (ASM), Change Controls, Chemical Engineering, Chemistry, Continual Improvement Process, Cost Reduction, Data Analytics, Electronic Components, General Hse Knowledge , Including Gdp, Knowledge Of Capa, Knowledge Of Gmp, Lean Manufacturing, Manufacturing Processes, Manufacturing Production, Pharmaceutics, Process and Cleaning Validation, Process Control, Process Engineering, Risk Management, Root Cause Analysis (RCA), Six Sigma, Standard Operating Procedure (SOP), Work Schedules